Reference story : Valio Aimo
Valio Aimo’s wholesale warehouses in Espoo and Kuopio are all-round distribution units. From the warehouses HoReCa customers can order practically anything they need at a hotel and restaurant environment. To become successful in wholesale business it takes not only a wide range of products, but also a 100 per cent availability, professional staff and efficient technology solutions.
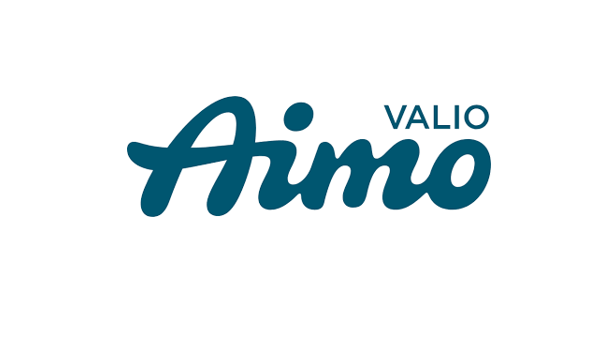
Co-operation with Optiscan kicked off in the early stages of the warehouse project. This way we were able to use their expertise for instance in WLAN installation and also in technical testing which needed to be resolved before the operation started. The collaboration has been running smoothly from day one.”
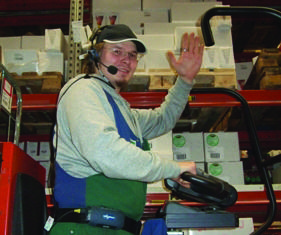
At the wholesale warehouse of Valio Aimo a pick-by-voice system supplied by Optiscan has been in use for years. The system is used for picking dry goods, frozen food, meat, vegetables and fruits. “Thanks to the pick-by-voice technology picking accuracy and quality have been improved and operation has become more straightforward. The pick-by-voice system guides pickers to perform right tasks in the right order”, says Jani Vainio, who is in charge for the wholesale warehouse operations at Valio Aimo.
As the company’s business and product range have been on a steady rise, they decided to build a new warehouse in Kuopio. Already in the planning stage a decision was made to learn from the example of the Espoo warehouse, where voice-directed technology and the operation models offered by the technology had proven to be reliable.
Jarkko Varpunen, Manager of Logistics in Kuopio warehouse, gives credit for pick-by-voice system. ”The goals for employees and the follow-up is now effortless. As the operation can be measured, we are able to anticipate the tasks of the incoming days better and estimate the number of the employees allocated for the tasks”, Varpunen states.
Photo: Minna von Weissenberg
Receiving of the goods, put-away and batch picking have become considerably faster. When the warehouse processes of the company run effortlessly, the customers are satisfied, too.
Pick-by-voice has made the training of new employees much quicker as well. At the same time the work safety has improved. Furthermore, the enhanced operation has had a positive impact on the environment. Due to the pick-by voice technology the carbon footprint has been reduced now that paper lists are no longer needed.
Thanks to the pick-by-voice solution supplied by Optiscan the new warehouse of Valio Aimo has become easier to direct and the whole order – supply chain is more efficient. Now Valio Aimo can concentrate on developing their own business.
Valio Aimo
Valio Aimo is a family-owned company, founded in 1899, which operates in wholesale business and import of daily consumer goods. The main customer group comprises food preparation and retail companies.
Optiscan Group
Optiscan Group has been providing solutions for warehouse management for over 30 years. The solutions are based on Voice and barcode technologies for enhancing logistics processes in warehouse, retail and healthcare logistics. We help companies to achieve improved efficiency and productivity by offering warehouse process management solutions. We are the market leader in Voice Picking solutions in the Nordic countries. Optiscan Group’s turnover is MEur 17+ and the company employs about 60 experts. Optiscan operates in Sweden, Finland, and the Baltic countries.
Get to know with our success stories
Optiscan Group – with a track record of successfully implementing Pick-by-Voice in numerous warehouses – was selected as the supplier of the solution for Medicarrier. Optiscan also supplied hand held terminals with bar code readers in order to handle goods receiving and shipping as well as transfers within the warehouse.