Reference story : Verkkokauppa.com
Verkkokauppa.com is the second biggest on-line retailer and webshop for consumer electronics in Finland. But how many have visited their warehouse? One could imagine that such a large warehouse would be extremely busy at all times – but actually it is quite the opposite, the atmosphere is calm and one might even say relaxed.
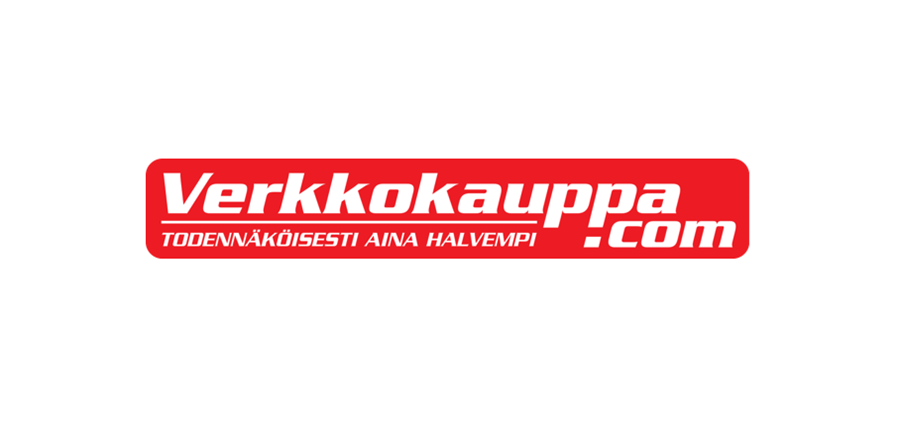
Since early times, we have been offering our products to customers through multiple channels, with the possibility to get the products delivered to their homes, offices or chosen pick-up points.
Henrik Weckström, CTO, Verkkokauppa.com
Voice Directed Work Calms Down the Warehouse
Verkkokauppa.com is the second biggest on-line retailer and webshop for consumer electronics in Finland. But how many have visited their warehouse? One could imagine that such a large warehouse would be extremely busy at all times – but actually it is quite the opposite, the atmosphere is calm and one might even say relaxed.
This was not the case earlier. Before a sales person would take in a customer order and then run straight to the warehouse to pick the products for that particular order. Nowadays the sales personnel can concentrate on customer service in the store and the warehouse staff takes care of picking, packing and delivery of the orders. Deploying voice-directed work was the calming factor.
“When we moved into our new warehouse we wanted to also renew our operations”, explains Henrik Weckström, CTO who mobilized the reformation of Verkkokauppa.com warehouse. “If the warehouse is not working properly, you can see the direct impact in the company´s financial result – and never in a good way. The costs for errors are high and the low productivity of manual work decreases the efficiency”, Weckström continues.
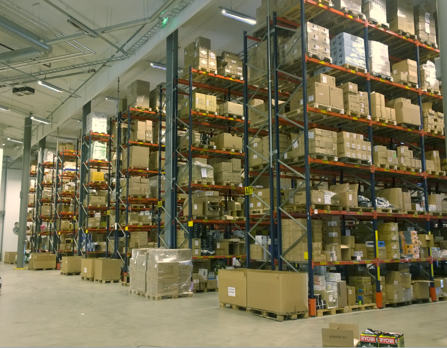
Nowadays operations in the warehouse are fluent and a big part of this smoothness is due to the Vocollect Voice solution delivered by Optiscan.
Customer Choices Drive the Process
Verkkokauppa.com offers consumers alternatives for purchasing their products. You can order on-line with delivery by mail or with a possibility to pick up the goods from the store. You can also buy or order directly in the shop. These diverse options set the bar very high for the picking system.
One distinct advantage of Pick-by-Voice provided by Vocollect is the possibility for batch picking or handling multiple orders at the same time. This means that the picker can pick up to 40 orders concurrently. Orders made on-line with the personal pick-up option are picked when customer arrives to the store. This sets up major demands for the picking system. All orders must be completed quickly and without errors.
Major productivity improvement is delivered by picking multiple orders with several products at the same time. When using pick-by-voice the picker requests new orders by using a voice command and receives instructions on the location of the first product. The picker then reads the check digit identifying the storage location and receives the pick quantity. The picker responds with the number of products that have been put on the carrier. The procedure is repeated until the order is finished and moved to shipping.
Multiple orders are handled in a similar way and products are put on to a customer specific position on the carrier until the last order line of the last order is finished. The equipment each picker is using consists of a headset connected to a compact Talkman terminal carried in a belt. All communication with the voice-application (which is the interface to the WMS-application) is wireless via Wi-Fi.
Verkkokauppa.com´s warehouse in Helsinki is very large. The actual stock space is 12 000 m2, and one specialty is that the warehouse is divided into 4 floors. This causes extra demands for warehouse systems, because the systems need to recognize product placements in different floors and the system also has to be able to bundle products on the same floor into the same picking batch. The extent of the operation – on average circa 100 000 order lines and on high peak Christmas season up to 150 000 lines per month – is challenging in many ways.
Less Errors – Higher Productivity
“Also our service level is now more consistent. Time used to complete one order is nowadays the same whether slow season or high peak”, says Heinonen. “One of the biggest advantages with the new system is the radical decrease in picking errors”, he emphasizes and continues: “Due to the check digits and confirmations in every phase of the picking process, making errors is extremely difficult. Before the changes we could have up to 10 picking errors per day, nowadays we have frequent error-free days. And even at most there are max 1-2 errors per day that is 90% less errors! This has happened largely due to Optiscan voice-directed picking solution, but of course general tidiness and better labelled aisles and shelves have some influence.”
“With the new voice-directed picking solution the time used for picking one customer order has been reduced by 50%”, tells Miika Heinonen, Logistics Director of Verkkokauppa.com
Remarkably Easy Implementation
The voice solution by Optiscan was integrated to Aptean IMI warehouse management system. “Never have we had such an easy integration project at Verkkokauppa.com”, emphasizes Heinonen. Voice was deployed already to the old warehouse, so after moving to new premises voice was familiar to the staff. “Co-operation during the project was extremely efficient – everything went by the schedule and things worked out extremely well. Also Optiscan´s project manager was constantly taking care of us and seeing through that we will also handle our own responsibilities according to the schedules”, notifies Heinonen. “The training provided by Optiscan and the support for the change management process were handled very professionally.”
Further Development Already Under Consideration
“At the moment we are using voice for picking”, explains Miika Heinonen. “But in the near future the pickers can use pick-by-voice system for example for checking the stock balance – not only for the certain picking location but for the whole warehouse. This way he can find out if the product he needs can be found on some other location. Productivity of the warehouse increases, when the picker avoids unnecessary visits to computer to check the stock balance. This idea originally came from one of our pickers, which proves that our staff is very committed in developing our operations”, emphasizes Heinonen.