Reference story : Medicarrier AB
Medicarrier is a supplier of all types of consumables for hospitals and other public healthcare organisations in Stockholm County. Pick-by-Voice has been used since spring 2010 for picking all goods.
Forklift trucks with multiple containers are moving fast on the warehouse floor in Spånga, outside Stockholm. Toilet paper, coffee, erasers, jumbo packs of paper for photocopiers and sterile consumables for surgery are picked and packed here.
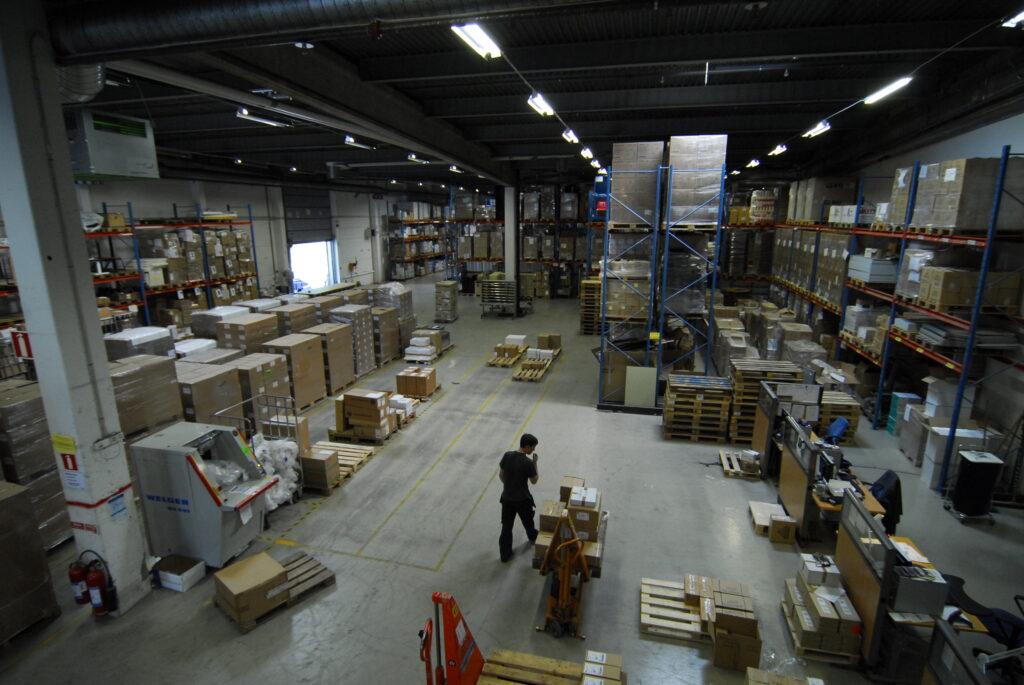
We are very pleased with Voice and the support we have received from Optiscan. We have easily been able to handle the recently increased volumes with existing personnel.
Håkan Runnstrand, Warehouse Manager, MediCarrier
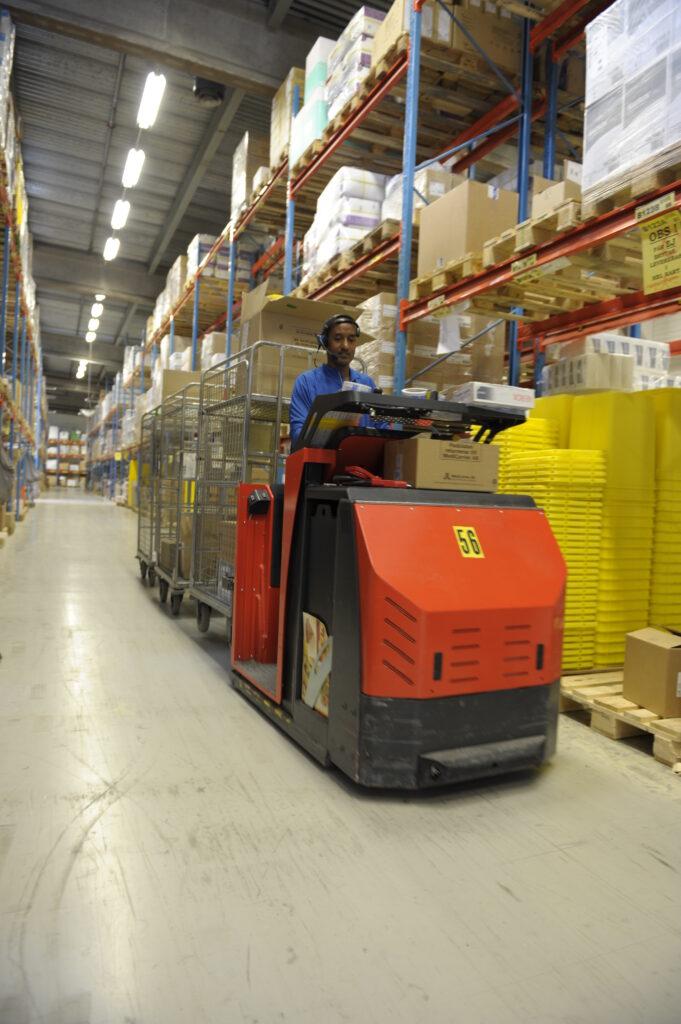
The 9000 square meter warehouse consists of the main area for picking with trucks and a sterile area for medical supplies.
Medicarriers warehouse is a highly efficient facility that supplies hospitals and other public healthcare organisations within the Stockholm County with all types of consumables. Approximately 6500 order lines are handled every working day by 35 pickers working in two-shifts.
The deliveries are coordinated, sorted and optimized, usually down to the exact end-user unit. – We have many customers at one specific hospital. “As we can coordinate our deliveries we can minimize both transport costs and the environmental impacts”, says Håkan Runnstrand.
Paperless system for picking and stock transfers
When Medicarrier upgraded their WMS-system from Aptean (earlier CDC Software) to a newer version they also implemented Pick-by-Voice. “We wanted to find a more efficient way for batch picking, picking multiple orders at the same time, more efficiently and minimize shuffling paper”, says Håkan Runnstrand. Improved ergonomics, increased efficiency and minimizing errors were the most important reasons for implementing Pick-by-Voice.
Optiscan Group – with a track record of successfully implementing Pick-by-Voice in numerous warehouses – was selected as the supplier of the solution for Medicarrier. Optiscan also supplied hand held terminals with bar code readers in order to handle goods receiving and shipping as well as transfers within the warehouse.
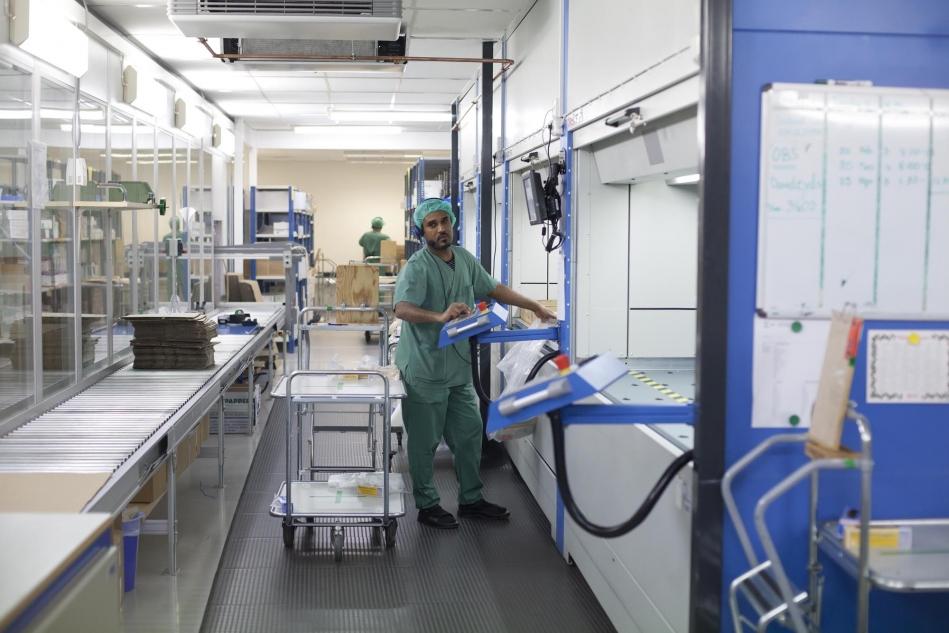
The many advantages of voice
The time for educating new pickers is another advantage, according to Håkan Runnstrand. The training time has decreased from 3-4 days to one day including, which now includes creating the voice profile for the new employee. Furthermore Medicarrier has also created a separate training area for the new pickers. In the beginning the employees had their doubts about the solution. “I think the main reason was losing the feeling of control that you may have when handling a printed pick list. But eliminating the pick list is the main key in order to increase efficiency and minimize errors”, he concludes.
Håkan Runnstrand is very pleased with the result of the project that, besides upgrading of the WMS-system and implementation of Pick-by-Voice, also included a major change of internal routines and physical rearrangements in the warehouse. In retrospect he concludes that the different parts of the project should have been taken in smaller steps in order to avoid problems during the running-in period. “We are very pleased with Voice and the support we have received from Optiscan”, says Håkan Runnstrand. “We have easily been able to handle the recently increased volumes the existing personnel”..
Get to know with our success stories
Optiscan Group – with a track record of successfully implementing Pick-by-Voice in numerous warehouses – was selected as the supplier of the solution for Medicarrier. Optiscan also supplied hand held terminals with bar code readers in order to handle goods receiving and shipping as well as transfers within the warehouse.